In tune with the development of technology, electromechanical processing is increasingly being chosen by more and more customers to create precise and highly aesthetic mechanical products. Let SUMITECH engineer learn these 2 methods to have the best choice for your processed products.
1. 2 current electromechanical processing methods
Electromechanical processing is an advanced and modern form of mechanical processing. This method is very effective with solid materials, processed in large quantities, creating high-precision products. Currently, there are 2 options for electromechanical processing. Specifically:
1.1. Electromechanical Machining (ECM)
This is a machining method based on Faraday’s law of electrolysis, creating surfaces with certain shapes by electrochemical etching. The finished product will not be subject to the mechanical impact of the tools on the machined surface.
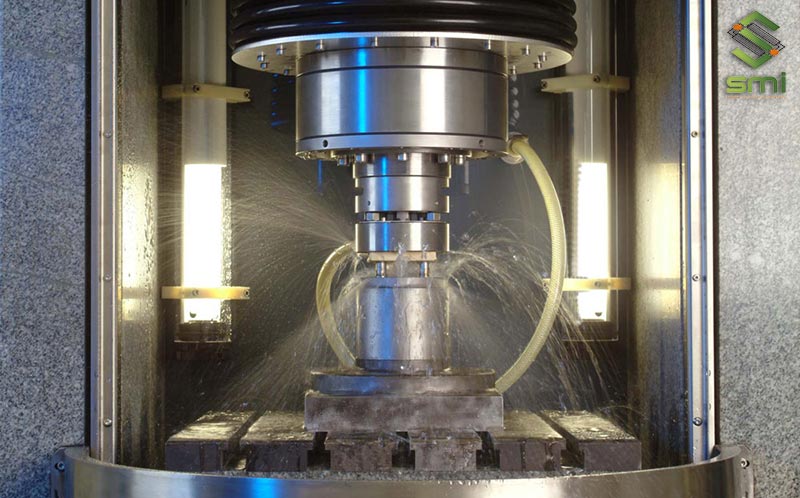
During the machining process, the positive pole of the current is connected to the work piece and the negative pole is connected to the tool. Two electrodes are placed in the electrolyte solution tank. Depending on the processing purpose, there are different corrosion processes to create the required product.
1.2. Electromechanical Machining (EDM)
This method uses two main components: the machine tool and the power supply. The machine tool closes to the profile electrode (which acts as a tool) and the electrode moves to the work piece surface creating the part according to the shape of the tool. The electric power source provides a high frequency, creating sparks between the electrode and the part surface, peeling off a layer of metal thanks to the vaporization and corrosion of the temperature.
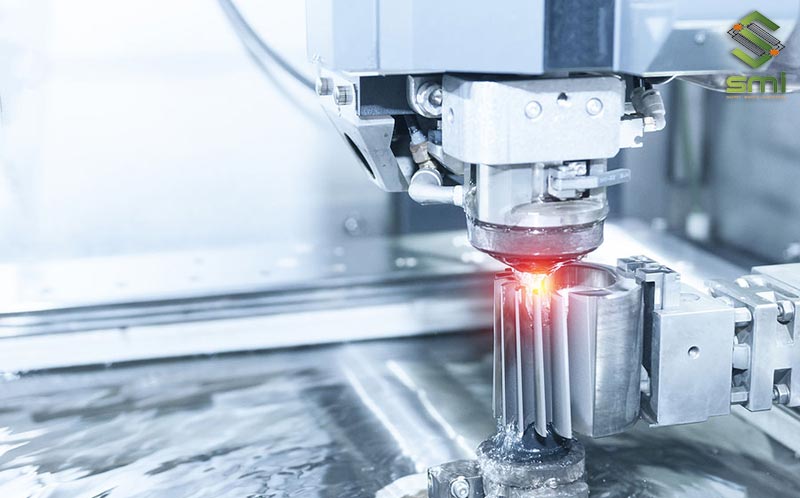
The accuracy of the machined product will depend on the accuracy and frequency of the electrode. Therefore, during the machining process, if the electrode is damaged, it must be adjusted accordingly for the machining process to be highly efficient.
Each processing method will have its own operating principles and different advantages and disadvantages. Let’s take a look at the pros and cons of each option in the following sections.
2. Advantages and disadvantages of each type of electromechanical processing
Knowing the advantages and disadvantages of each type of electromechanical processing, businesses will quickly choose the optimal plan for each product.
2.1. Advantages and disadvantages of electromechanical machining
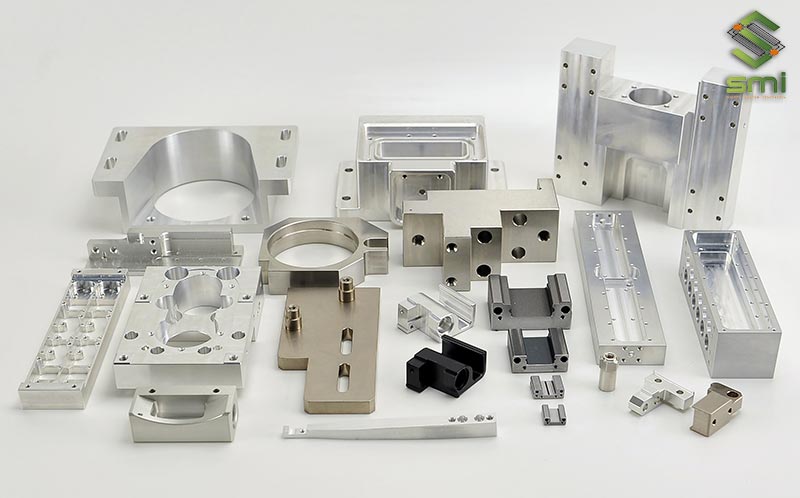
Since no impact tool is used, this method is very popular. Besides, there are countless outstanding advantages:
- Can be polished inside and out with all different shapes
- High processing capacity and limited manual labor
- The processing equipment is cheap and simple, so the processing cost is low
- Surface quality is more improved
- Polishes hard surface materials
- Does not change and deform the surface layer structure
- Ability to automate in the machining process
- The environment and working conditions of workers are improved
However, using this method should also note the disadvantages:
- Limited life of electrolyte solution
- Keeping the correct size and shape is limited
- Apply only to not too rough machined surfaces.
2.2. Advantages and disadvantages of electromechanical machining
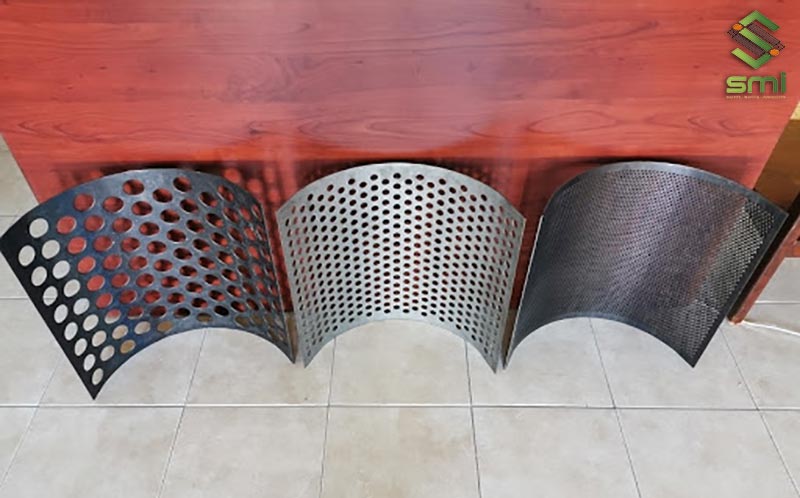
Different from the above method, electromechanical processing has the following outstanding advantages:
- Machining materials with various hardness. Even with soft, fragile materials without fear of deformation.
- Electrodes can be reproduced in any shape, fabricated and restored with hardened steel dies.
- Application to make sieves, sieves, with very thin electrodes
- Machining to produce products with very small diameter holes, deep holes with a large length to diameter ratio.
- Due to the use of oil when processing, the machined surface is tempered in oil to create a shiny product.
Businesses also need to note some disadvantages:
- Requirement for workpiece and tool (electrode) to be conductive material
- The workpiece before machining when the electrode must be roughened first because of the low cutting speed
- Causes thermal deformation by high temperature working area.
3. Application of electromechanical machining and electromechanical machining
With the above advantages, these two processing methods are widely applied in many manufacturing industries.
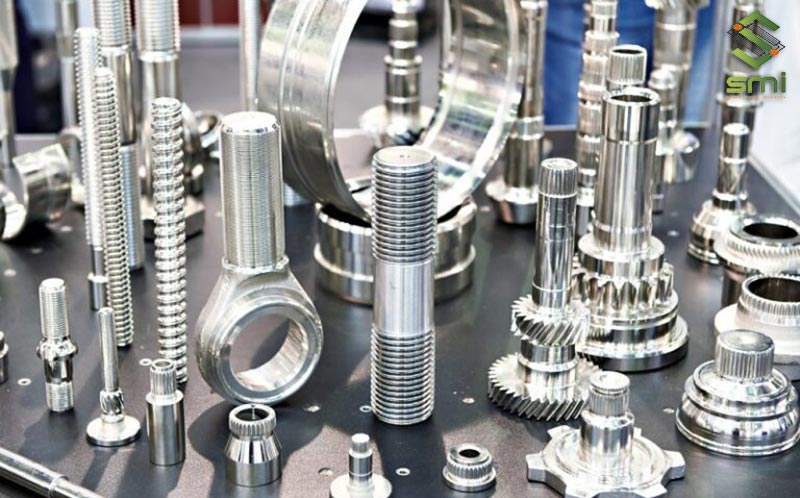
Applications of electromechanical machining:
- Processing and shaping products with complex spatial structure with materials such as heat-resistant, wear-resistant steel and stainless steel. The most characteristic is the turbine blade.
- Machining parts with small holes (from 0.3mm) by the precision of electromechanical machining of pores is 0.02-0.03mm.
- Processing many products with high productivity. Because the two machining electrodes have a speed of e = 1.18mm/min, the machining process only takes 5-10 minutes. If this is done on a manual grinder, the finishing time can take up to an hour.
- Crafting details with deep holes, small size. And will achieve optimal economic efficiency if processing batch, large quantity.
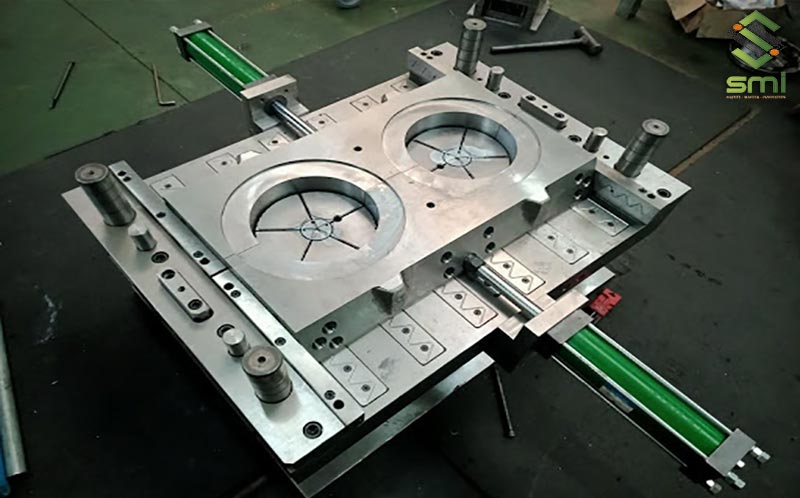
Application of mechanical processing of electrodes
- Increases the abrasiveness of the products by increasing the surface hardness of the part.
- Fabrication and restoration of hard alloy molds, hardened stamping dies
- Machining to make sieve mesh holes, sieve by thin electrode
- Perform flat grinding, round grinding, sharpening or hole widening
- Machining holes with a small diameter of 0.15mm of high-pressure nozzles with high productivity (about 15-30s/piece). Or process holes from 60mm deep (with low tolerance), as small as 0.05-1mm in diameter as the cooling holes in turbine blades.
- Application to pick up broken tools, clamp in bolts, taps, etc.
- Mold processing with hard alloy material, high precision.
4. Should I choose electromechanical processing or electromechanical processing?
Each processing method brings different results. Therefore, depending on the desired processing product, businesses should consider carefully to choose the appropriate method. If you have any doubts, please contact reputable units in this field for advice.
One of the professional processing units, receiving a lot of attention from customers today is SUMITECH Industrial Joint Stock Company. SUMITECH has more than 10 years of experience in the field of mechanical processing. With practical knowledge when participating in many different projects, SUMITECH will advise the best and most economical method for customers.
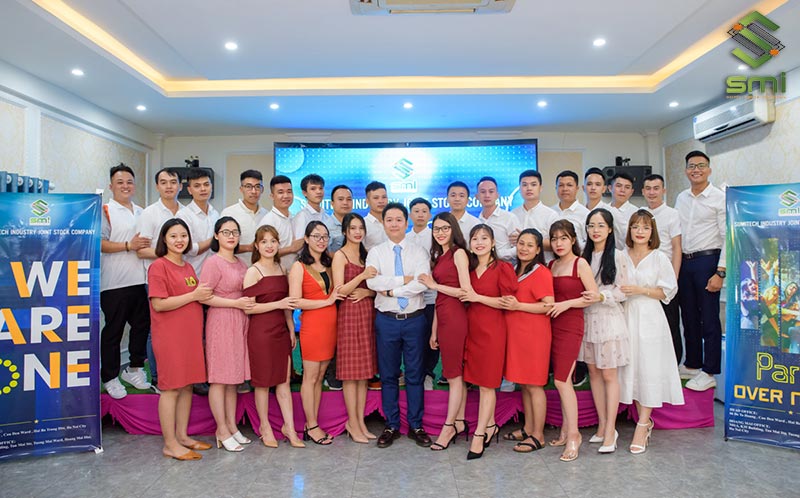
- Customers who have cooperated with SUMITECH:
- Factory in North Thang Long Industrial Park
- Factory in Dong Van Industrial Park
- Factory in Dai Dong Industrial Park, Tien Son, Que Vo
- …
For more information and specific advice on electromechanical processing services , please contact SUMITECH for dedicated and thoughtful advice.
- Hotline: 0989.060.987 – 0986.656.152
- Email: info.sumitechvn@gmail.com
- Fanpage: https://www.facebook.com/sumitech.industrial.jsc